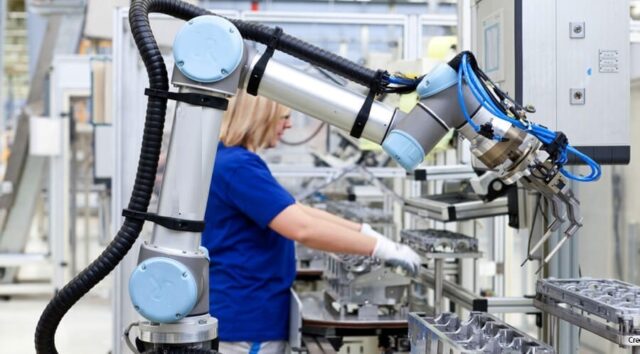
An assembly line is almost always used by companies that manufacture whole items. Assembling is where they put all of the individual parts together, screw or apply glue to seal to achieve a finished product. However, it is becoming more difficult to find and maintain a reliable workforce over a long time. It may also become more difficult for current employees to achieve results at the appropriate rate.
As a result, assembly tasks are increasingly becoming automated. Human-robot collaboration continues to progress with the development of collaborative robots that can operate together with humans. Using a robot in an assembly line to boost overall production is now quicker, less dangerous, and faster.
A collaborative robot is easily programmed to do a specific activity without needing to be gated off from the rest of the environment.
Each organization that assembles as part of its production process adopts automation to meet its unique production requirements. Fortunately, efficient collaboration robots have helped enterprises attain optimum efficiency.
5 Factors that make Cobot Use in assembling Possible
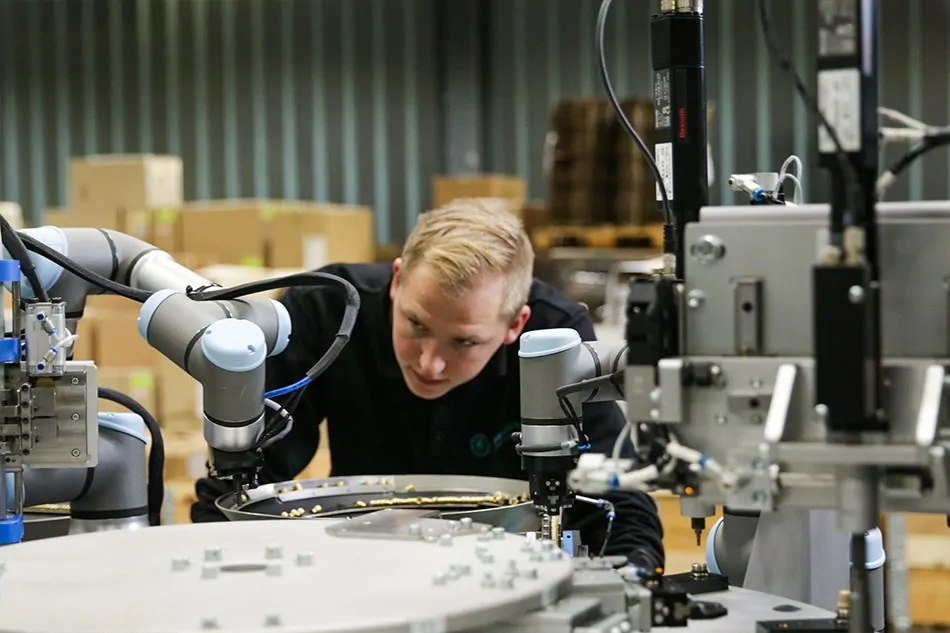
1. Repeatability
The robot’s assembling motions must be consistent. Nevertheless, with fragile materials such as circuit boards, exceptional precision is required to generate high-quality products and avoid damaging the pieces during the assembly operation. To do this, one must select an optimal robot configuration that meets the application’s repeatability requirements.
2. Payload
It refers to the maximum weight that the robot can safely carry. To establish the robot’s payload, assess your device and the toughest part you intend to transport.
Analyze the heavy machinery or other active tools and have a large mass since the robot must surpass this burden. When applying force to a part, keep in mind the cobot’s maximum payload rating.
3. Rotation
The robot will sometimes need to take part from one location and position it in another (picking and placing). The distance between the two places must then be measured and divided by two. It informs you of the cobot’s bare minimum reach.
Because a greater robot is more powerful, the payload will inevitably grow for a long reach. When screwing apart, make sure the robot’s wrist can rotate indefinitely.
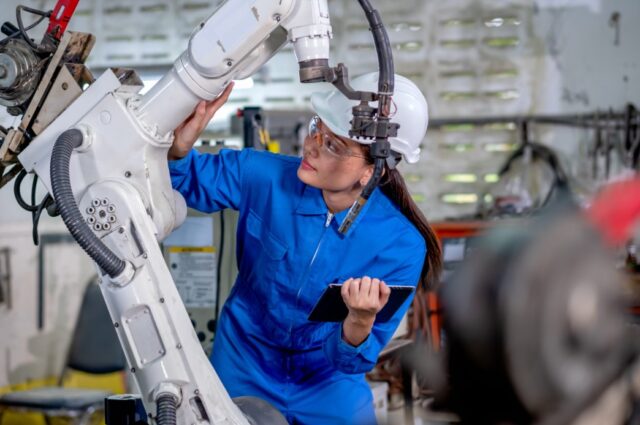
4. Mobility
When changing manufacturing, it may be necessary to shift the robot occasionally. Collaborative robots are often powered by 120V electric energy directly from the socket. With a rolling foundation, it may be moved wherever it is needed.
All that is required is to connect it to the new place and update the programming for the new process. If you want the cobot’s position to be repeatable, stabilize it. If you wish to keep relocating the robot to fixed locations, make sure there are physical stops or anchors to clip the cobot.
5. Safety
Although the collaborative robot operates effectively amongst people, it is still necessary to do a risk assessment before initiating the robot because it still poses a risk. It is important to remember that although the cobot is safe, it can still be dangerous if it bears a sharp object.
How Collaborative Robots Are Maintaining Safety in Assembly Activities
Human safety in the assembly workplace is crucial since an accident is detrimental to the workers hurt and the management, who may incur losses due to litigation cases. Therefore, it’s important to know the measures in collaborative robots features to ensure this does not happen.
The latest generation of robots contains unique safety features, such as software embedded in collaborative robots that allows them to reduce the risk of harming their human counterparts. It can evaluate a zone and mark it as a safe zone.
Here are Three Essential Safety Precautions Taken by Cobots
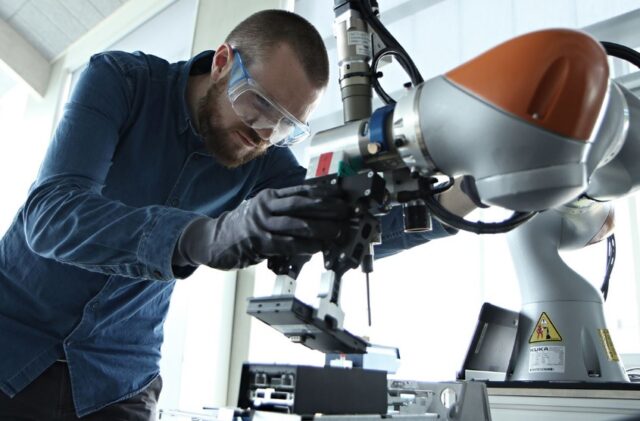
The Predetermined Safety zones
When the robot is in the exact zones configured to do so, the dedicated safety zone permits it to limit its working speed. Workers configure it by specifying the region and optimum pace of operation, lowering the risk of an accident.
Zone of Variable Safety
The cobots in this zone are equipped with a visual system that monitors their surroundings. The operator can then select each zone’s various zones and related speeds.
When someone approaches the zone, the robotic arm tends to slow down; as the person gets closer, the robot’s pace will lessen until the human reaches the nearest potential zone, at which point it will come to a complete stop. When the robot leaves the zone, it will return to its usual pace.
Hand Guiding
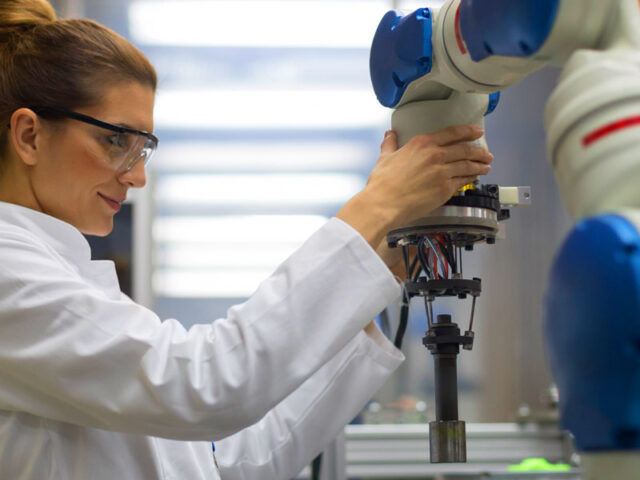
Another safety element in the robot’s model is the hand guiding feature, which allows people to control the robot for programming and set the courses they would like it to follow.
The software allows the robot to move in a zero-gravity state, allowing users to maneuver it without harming it freely. It makes programming the robot arms extremely simple and secure. After the worker completes the manual guidance procedure, they will hit a button on the cobot’s interface, and the robot will begin performing the task.
Each of these collaborative operations features safeguards users distinctly. For example, in the fixed protection robot assembly vicinity, you offer protection by not enabling the robot to move when a human is in the shared workspace. In contrast, you protect people for hand guidance by authorizing the cobot to function at full speed only when the operator controls the robot’s movements.
UniversalRobots has addressed the issue of safety by designing robotic technology with control functions that can identify people to assure a high level of integrity, preventing collisions and injuries.
There’s also the in force and power limiting, which ensures that the pressures imposed on someone’s body if they contact it are minimal enough to be considered minor. However, because some regions of a person’s body are more sensitive than others, this may vary.
Final Remarks
Collaborative robots are a perfect development in the overall robotics field, as seen by their rising acceptance by various businesses worldwide. Because cobots are simple to operate, they keep control of assembly automation systems in the presence of human workers, allowing firms to redeploy creative processes away from dull and risky occupations to more value-added tasks.