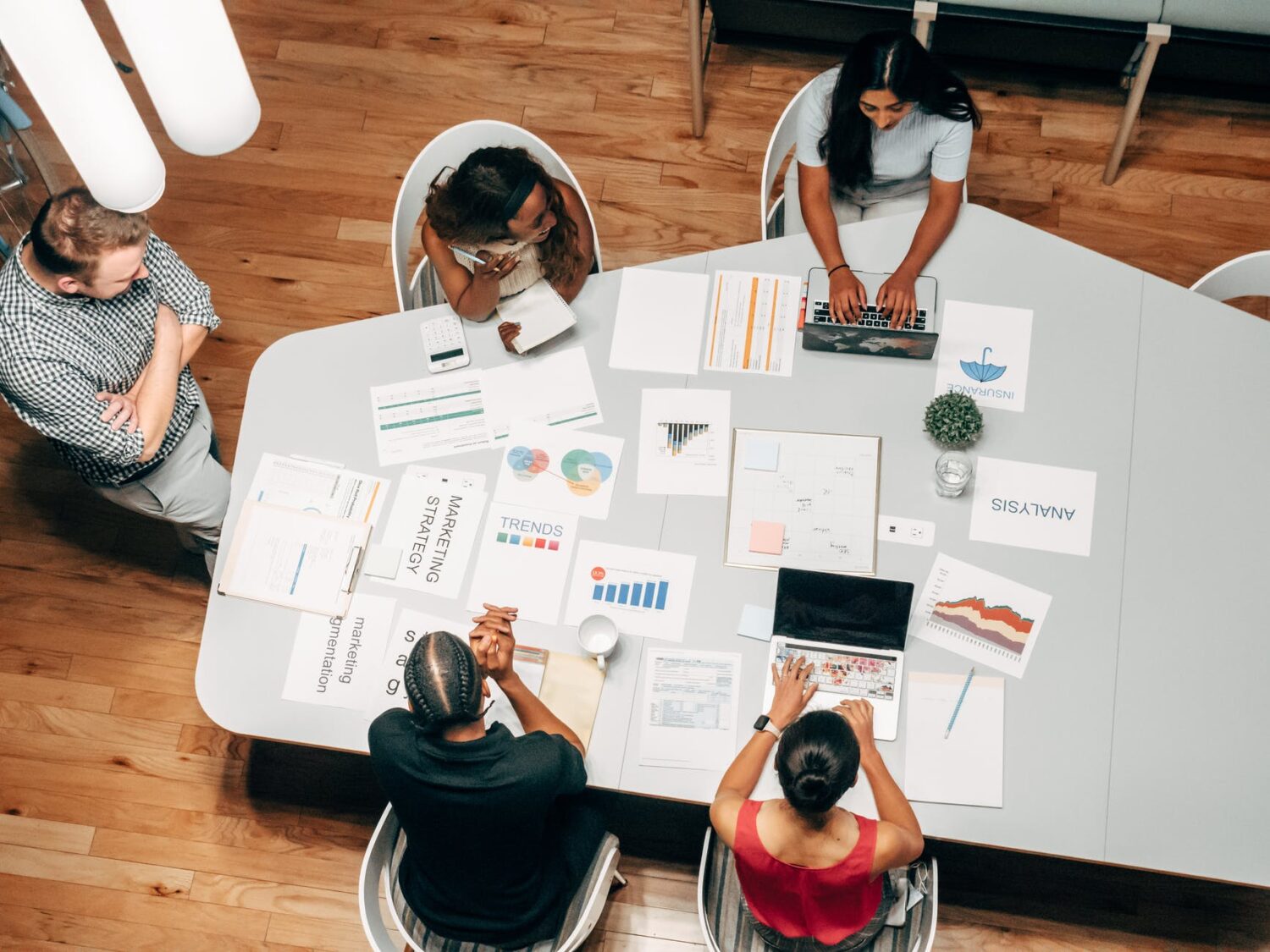
The major task of all companies that are using chemical products is that they need to produce adequate chemical safety details that are in accordance with regulations.
However, the biggest mistake regarding this topic is that companies sometimes have problems with interpreting regulations as well as with implementing processes to sustain chemical compliance. Since they are faced with everyday challenges and obstacles, they frequently make some mistakes.
In this article, we are going to discuss some of the most common mistakes that are made regarding SDS management and authoring. In that way, companies can focus on them and find a proper solution that they can execute. Only in that way, companies can run their business in the most ethical way and businesses owner can be peaceful that every work they are doing is according to the strict measures and regulations.
We must mote that statistics show that so many employees die from toxic chemical exposure across the world. This is the most crucial reason why prevention with the proper training and careful handling can affect ideal SDS management practice. In that way, fatalities of this kind can be avoided including the minimum risk of their occurrences.
Nowadays, if you are running a company that is working with toxic chemicals, it is necessary to be aware of the consequence and to do everything you can to prevent them, and avoiding mistakes is the most significant step to achieving that goal!
The first mistake – Company is Failing to Make SDS Sheets Accessible
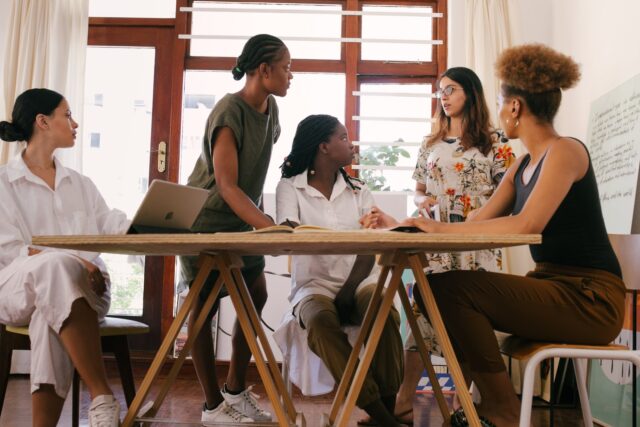
Everyone needs to realize that safety data sheets are formed that some company needs to fulfill with a detailed explanation of the hazardous chemicals that exist around the workplace. Only in that way, all employees of some organization can be aware of the potential consequences to their health and protect themselves against the hazard at the workplace. Logically, prevented protection is crucial when it comes to keeping people from getting hurt. On the other hand, a particular company can even benefit from SDS sheets that contain a detailed list of hazardous chemicals in addition to preventing lawsuits against them. OSHA requirements are dictating that SDS sheets need to be accessible to all employees all the time and to sustain accurate information.
Logically, workers need to be able to find the SDS sheets very easily and examine them at any time they think there is a need for that. This means that you need to save this document in a location that all workers know about and have easy access to it. In general, you should know that digitizing documents makes the whole procedure of accessibility easier.
Therefore, you can consider keeping SDS sheets in a management program that all workers can access through some device whether it is a desktop device at work, tablet, or via mobile phones. This practice will give your workers the chance to prepare themselves better for the workday. They will be able to check chemicals while they are still at home and after getting to know all the facts, decide what is the best way to prepare themselves for the outcoming workday.
The second mistake – The company do not use adequate SDS Software
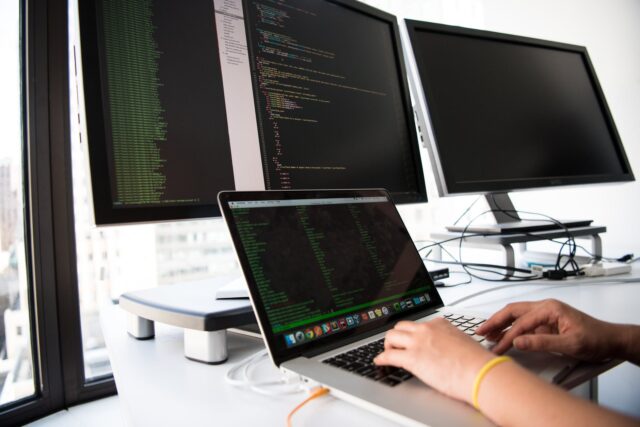
We understand that SDS management can be an incredibly challenging procedure. This especially counts for the documentation that includes all hazards within a particular section. However, it is noticeable that in many organizations last users that have the job of tracking chemicals that they got from the manufacturer are struggling frequently with the delivered documentation. This can lead to a big problem since those workers will have trouble keeping up and understanding new information that is found on the chemical topic. However, there is a tool precisely called SDS management software that can be able to help with this type of problem and make the overall work of the end-users when it comes to filling out these chemical segments.
The right SDS management software function on the principle of saving all details from other related chemicals, so the workers will have a clear insight of all accurate data they need to read carefully. One high-quality benefit of SDS software management is that keeps storing and backing up data effectively. The job of the workers in companies of this kind will be much quicker and more convenient.
Best of all is that this software can reduce the possibility of human error occurrences. If you are interested in investing in SDS management software today and keeping all the SDSs data up-to-date click here and consult with the company that is committed to helping you become a much safer workplace by documenting and recording all of the hazardous materials.
The third mistake – The company is failing to comply with OSHA regulations
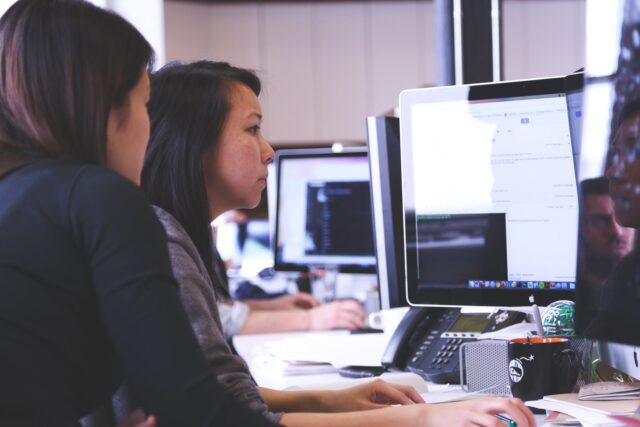
Unfortunately, even the high aware companies that have the right SDS technology system can have problems and struggle with accurate timely updates. If the company does not keep its SDS sheets up to date, it risks facing heavy penalties from OSHA in case they request your report. Since your company probably does not want to risk getting in this kind of situation, you need to make sure that you are obtaining manufacturer-authored SDS sheets for new chemicals right after your company starts to work with them. In other words, you need to be responsible and immediately react and report all new chemicals that your company is using and working with at that point. The key to good business is to update new information. In that way, you will not have to worry about getting any type of fines.
The fourth mistake – The Company Do not file out labels properly
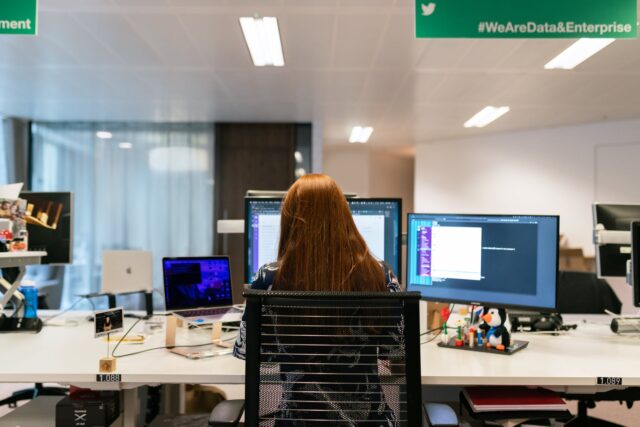
When it comes to the job of filling out labels on time, it is important to do that job in an accurate way. In case you do not fulfill all possible sections of a GHS label, you are risking putting all of your workers and everyone that comes in contact with the chemicals at risk.
Additionally, you are risking getting fines from the OSHA organization because they do not tolerate mistakes of this kind. Appropriate labeling is the key to a successful business.
Therefore, make sure that you are controlling GHS label management and that all sections are filled out properly. Logically, all necessary information and international warning symbols need to be included as well.